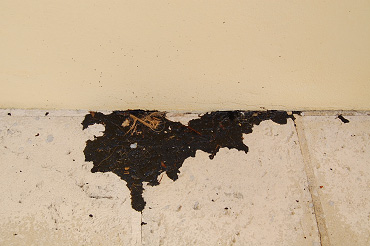
Saponification of waterproofing material: Is there trouble just beneath the surface?
By Peter Craig
After 25 years involvement with exterior waterproofing in Florida, I am very aware of how dynamic this area of construction is. New products and techniques are constantly developed to meet market needs and niches. However, not all new products or methods have performed as anticipated. The result is that some waterproofing systems and installation methods have evolved through learning from our collective mistakes to what they are today.
When dealing with forensic investigation of older waterproofing applications, we have to bear this in mind when we evaluate the problems. The system may have been correctly installed per the recommendations and industry standards at the time, although the standards have since evolved.
One example is concrete repair over this period. The last 25 years has seen many new products introduced, seen repair methods evolve from “patches” to “repairs”, and the establishment of the International Concrete Repair Institute (ICRI) to help set and maintain industry standards.
Another is the waterproofing of plaza decks. About a decade ago, the acceptable “standard” within the waterproofing industry for plaza decks included using cold fluid-applied emulsion or polyurethane coatings, and did not include a drainage board or drainage mat. There was concern that a drainage layer would act as bond breaker.
If a drainage mat was specified it was often a budget cut victim.
Structural decks were to be sloped. Placed between the structural slab and the various topping slabs, planters and curbs, the waterproofing was considered sandwich slab waterproofing, and where adequate sloping could not be achieved, the waterproofing was applied to the topping slab. Drainage was based upon the water wicking through the concrete overburdens to the drains or through the sand setting bed beneath pavers. The exposure of the plaza deck would allow for evaporation as well.
However, the collective lessons quickly learned were that most large decks do not drain perfectly so water “stands” on the waterproofing for extended periods of time, that the lack of a free flowing drainage plane requires the overburden (sand, topping slab, setting mortar, etc.) to become fully saturated before the water begins to effectively wick away, that these saturated materials take longer to dry out, and that climate conditions (e.g. daily thunderstorms) can affect drainage and evaporation. The result was that it was not long before drainage mats were recommended over the waterproofing and hot fluid-applied waterproofing have become industry standards for covered horizontal deck waterproofing.
But what of all the decks that were waterproofed during that period? The old standard was also based upon the belief that once cured the waterproofing product or protection board would remain stable for the life of the system or at least the warranty period. Has the lack of a drainage system caused other types of problems to the waterproofing systems? The answer is yes, with major renovations and expense required to correct them.
I first saw the potential damage about 2 years ago on a vast recreational plaza deck over a parking garage in Southeast Florida. Waterproofing materials were bubbling up from beneath the pavers (Photos 1 & 2) all over the deck, and dripping into the parking garage below (Photos 3 & 4) – although there were no reported active water leaks.
Photo 1Photo 2
Photo 3
Photo 4
During a mock-up repair installation, a manufacturer’s representative provided an explanation. The breakdown of the waterproofing material was “saponification”. It was a chemical reaction in the waterproofing product triggered by the “standing water” on top of it. The result was that the product became a new material with different performance characteristics.
Visible indicators of the “saponification” of the waterproofing material included visible “oil slicks” on the surface of surrounding water (Photo 5) as oils and surfactants left the membrane, the increased thickness of the waterproofing membrane (Photo 6) as water molecules replace the oils and surfactants lost so that water can be squeezed out of the swollen material (Photo 7), and the change in chemical composition causes loss of the waterproofing bond/adhesion to the substrate (Photos 8 and 9).
Photo 5
Photo 6
Photo 7
Photo 8
Photo 9
With the asphalt/bitumen based products (e.g. protection board) the oils re-emulsify and leach out of the product (Photos 10 and 11)
Photo 10
Photo 11
Photo 12
The source was credible and the explanation fit the characteristics witnessed. However, in providing a ready explanation, it confirmed suspicion that the failure of cold fluid-applied waterproofing as a result of standing water was not unknown within the industry. The explanation also provided insight into other areas of failure previously seen on other projects and those that were seen subsequently (Photos 13, 14 and 15).
Photo 13 – asphalt oils from the protection board leached into paver setting sand
Photo 14 – delaminated and blistered polyurethane membrane
Photo 15 – pock marked waterproofing membrane
A secondary source of confirmation or agreement with the “saponification” explanation was desired but extensive internet searches found little direct discussion with regard to failing waterproofing products on plaza decks. This was not unexpected given the potential liability to manufacturers. However, based upon the information read about saponification, polymers, and emulsions there are pieces of information that combined appear to support the explanation.
The key information items I have read are:
- Saponification is commonly used to refer to the reaction of a metallic alkali (base) with a fat or oil to form soap.
- Petroleum based products can contain additives that react with alkali to form (metal) soaps. Fats are examples of such additives. ASTM D94 – 07 Standard Test Methods for Saponification Number of Petroleum Products expresses the amount of base that will react with 1 g of sample when heated in a specific manner.
- Asphalt (U.S. terminology) and bitumen (outside U.S.) are the same – both are developed from crude oil.
- An Emulsion is a mixture in which solid particles are suspended in a liquid in which they are insoluble, with uniform dispersion of the particle globules. Oil and vinegar salad dressing is a simple example. Many waterproofing products like bitumen/asphalt based products are emulsions as well. The product cures or reacts as the liquid (often water) evaporates to become waterproofing.
- Polyurethanes are produced by the reaction of a polyisocyanate with a polyalcohol (polyol) in the presence of a catalyst and other additives. Isocyanates react with water (or any molecule that contains an active hydrogen) to form a urea linkage andcarbon dioxide gas.
- Surfactants are used with both emulsions and polymers to modify characteristics, to emulsify the liquid components, to regulate cell size, and stabilize the cell structure to prevent collapse and surface defects during the application process.
- Emulsification is an all-or-nothing event. If the mixture fails to emulsify to a stable state at the start, no further adding of ingredients will aid it. Conversely even though a mixture has successfully emulsified it can re-emulsify years later. This is particularly true if the liquid used (water) is reintroduced.
- DOT studies of highway bitumen or asphalt products indicate that these products can become unstable and/or breakdown under the right conditions – a combination of standing water, high alkalinity and hot temperatures resulted in the product re-emulsifying and breaking down.
Most cold fluid-applied waterproofing membranes are emulsions or polymers with surfactants added and water is the key dispersal component. Summer provides regular saturating rains and prolonged water immersion which can result in these products re-emulsifying, and creates the high surface temperatures. The saturated lightweight concrete, mud set and even the pavers are all potential sources for providing high alkalinity to the standing water.
As a result 10 or 11 years later, there is a “generation” of buildings with plaza decks (particularly in Florida and South Texas) that have waterproofing products and applications that met industry standards at the time of installation, but have all of the elements and conditions to potentially experience or are experiencing this type of waterproofing failure. However, the trouble may be hidden beneath the surface until the product has broken down enough to leak, ooze out or stain the surrounding surfaces.
Keep your eyes open, and please contact Glazing Consultants International, LLC, if you have any questions.
Peter R. Craig specializes in the exterior waterproofing of exterior walls, decks, and below grade areas. Born and educated in Cape Town, South Africa, he has been with Glazing Consultants since 1997. He has over 25 years experience in the waterproofing industry in both new construction and restoration waterproofing. He combines his extensive knowledge of products, techniques and his practical experience to provide answers, solutions, guidance and long term maintenance programs. His expertise includes stucco, EIFS, vertical wall coatings, expansion joints, concrete repair materials, deck membranes and sealers, and sealants. Peter can be reached at pcraig@glazingconsultants.com or on Twitter @glazingconsult. Find out more about GCI at http://www.glazingconsultants.com, and join our Building Envelope Matters LinkedIn group to discuss building envelope issues.