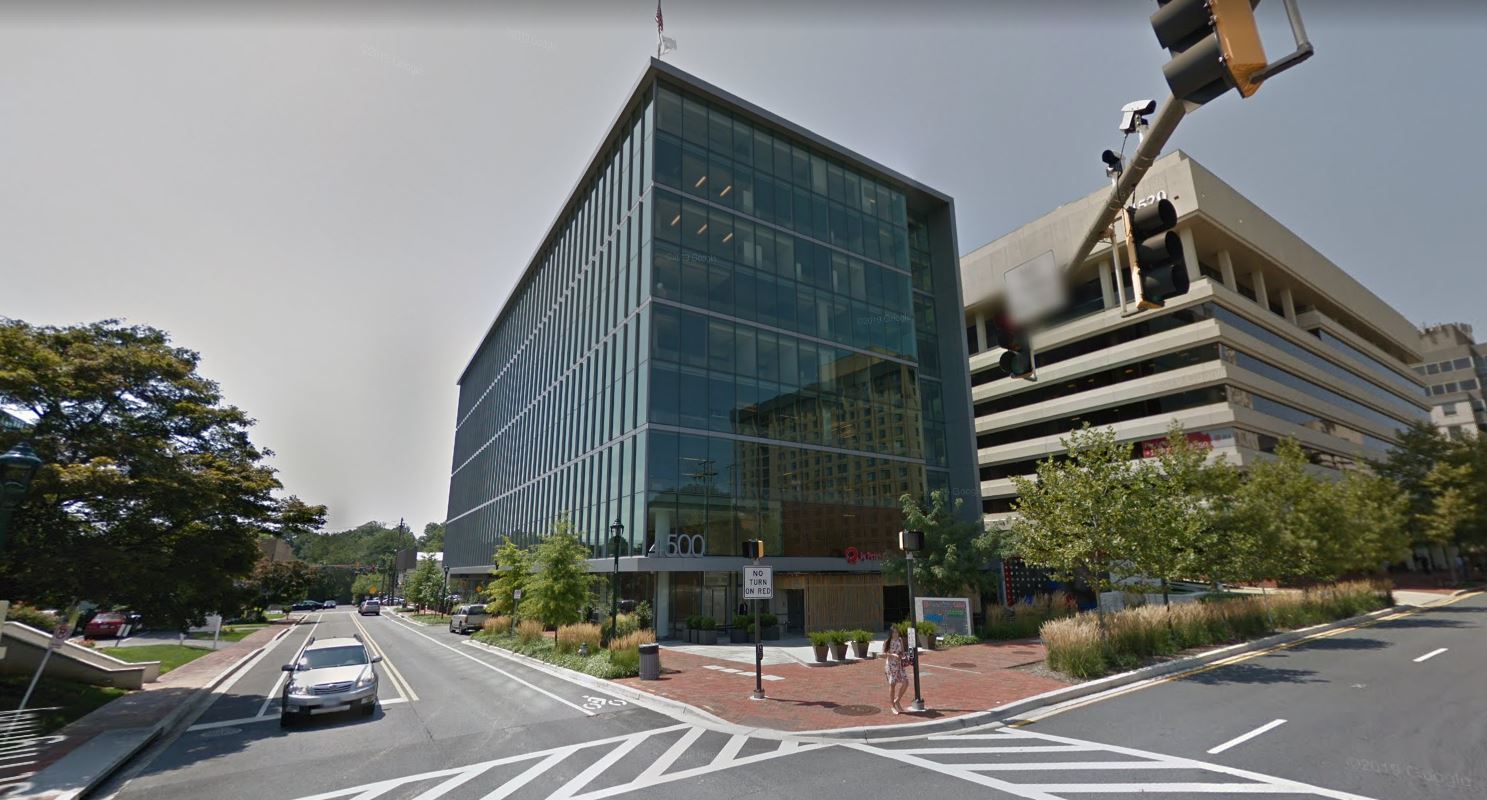
Paul Beers Quoted in Washington Post Article
Protective scaffolding surrounds a nine-story glass office building in downtown Bethesda where pieces of glass have fallen onto sidewalks. Montgomery County officials ordered that the scaffolding be installed in February to protect pedestrians from falling glass. (Katherine Shaver/The Washington Post)
The owner of a nine-story office building in downtown Bethesda has agreed to replace part of its glass facade, saying that a manufacturing defect caused glass panels to break 11 times and, in at least three of those cases, fall to the sidewalk below, according to two reports filed with Montgomery County.
Hadi Mansouri, the county’s acting permitting director, said his office reached an agreement with D.C.-based Carr Properties on Tuesday to replace the problematic tempered glass on its building at 4500 East West Highway, just east of Wisconsin Avenue.
The building, which opened in 2014, has had scaffolding protecting the sidewalks around it since February, when Montgomery permitting officials ordered it as a safety precaution. That followed what county officials said had been at least the third incident since April 2017 in which broken glass had rained down onto the sidewalk.
No one was injured in any of the incidents, but some pedestrians reported close calls with falling glass. The sidewalks are frequently used by office workers and students from Bethesda-Chevy Chase High School across the street.
Drawings in a report that Carr’s engineering consultants filed with the county show 743 panels on all sides of the building with the type of glass that the company said has shown flaws.
However, Dominique Daschle, a Carr vice president, said Wednesday that Carr is still trying to determine whether the manufacturing defect can be isolated to a “certain batch or other conditions” to limit the number of replacements. If it can’t, she said, “we would look to replace all” of the type of glass that has shattered.
“We continue to work diligently toward a permanent solution, though none has been finalized at this time,” Daschle wrote in an email. “This includes developing a plan to replace all or some of the windows in an expeditious manner.”
Carr declined to make anyone available for an interview.
A study found that the breaks were “spontaneous” and caused by nickel and sulfur impurities getting into the tempered glass during manufacturing, according to a report by Carr’s engineering consultants, KCE Structural Engineers and Simpson Gumpertz & Heger.
Such imperfections, which are “undetectable,” can cause glass to break spontaneously, Daschle wrote.
Paul Beers, a glass expert for his West Palm Beach, Fla., company, GCI Consultants, said nickel and sulfur can become a “relatively uncommon” problem in glass that has been heated to make tempered glass. Often called safety glass, it’s designed to break into little bits on doors and in other ground-level areas where people can accidentally walk into it.
After the impurities are heated, Beers said, they expand over time and can cause the glass to shatter, often after the sun has hit it from a certain angle.
Potential problems with spontaneously shattering glass have led many building owners to forgo tempered glass in upper stories, he said, because it becomes unstable under its own weight, causing glass to fall out. He said the alternative is laminated glass, similar to that used in vehicle windshields, which is designed to stay in place when it breaks but is “significantly” more expensive than tempered glass.
“It’s really not appropriate to use [tempered glass] on a high-rise building,” Beers said. “It doesn’t have any stability if it does break.”
Daschle said the building code required safety glazing on the glass because it extends from floor to ceiling. Tempered glass met those code requirements, she said.
Mansouri, the acting permitting director, said the protective scaffolding will remain in place until the glass work is complete.
Reaching an agreement with Carr “wasn’t an easy job,” Mansouri said, “but they agreed to do the right thing for people’s safety.”
Daschle said Carr has not determined how much the panel replacements will cost or who will pay for them. She also declined to provide the name of the glass manufacturer.
Bethesda-based Clark Construction built the “all-glass curtain wall building” for $39 million, according to Clark’s website. A Clark spokeswoman referred questions to Carr.
The original article can be found here.
Learn more about GCI Consultants.