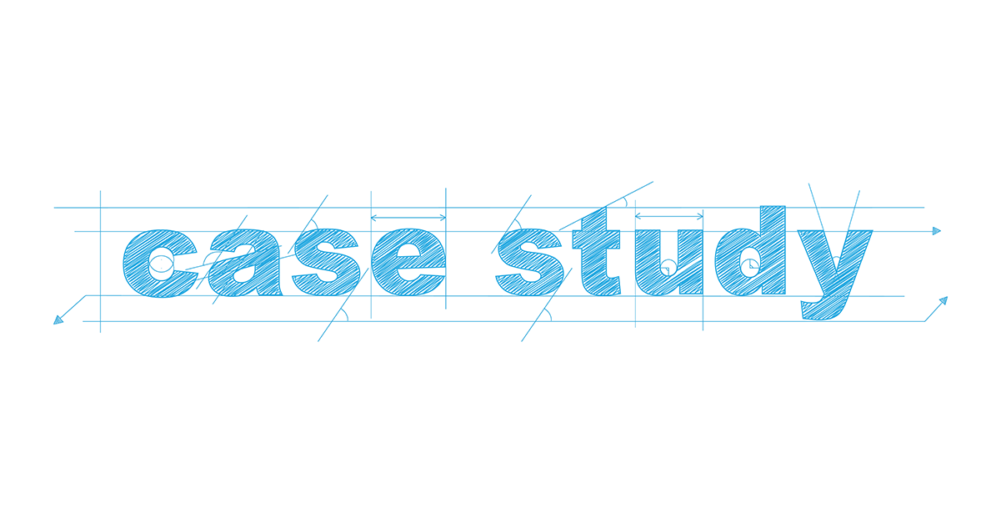
Case Study: Forensic Water Intrusion Investigation at a South Florida Hotel
This detailed case study highlights how GCI Consultants conducted a forensic water intrusion investigation to address a complex water intrusion issue at a South Florida hotel, focusing on roof membrane failure and EIFS vulnerabilities. Overall, it demonstrates problem-solving, sustainable remediation, and best practices in building envelope maintenance.
The Challenge
GCI Consultants was engaged to conduct a forensic water intrusion investigation of reported leaks at the upper floors of a hotel building in South Florida. Heavy staining and moisture damage were observed around ribbon windows on the top two levels, resulting in guest complaints, room closures, and revenue loss. Notably, lower floors with identical windows showed no evidence of major window leaks, suggesting a localized building envelope failure.
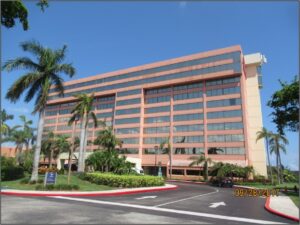
Staining observed around windows on upper levels.
First, a preliminary moisture survey revealed significant water ingress through the single-ply TPO roof membrane. It was determined that the metal stud-framed parapet walls and the barrier EIFS (Exterior Insulation and Finish System) provided a pathway for water to travel from the compromised roof areas down into the window heads below. As a result, roof replacement and further investigation into potential wall system deficiencies were recommended.
The project’s purpose was to develop opinions on the apparent conditions of the building’s exterior walls and glazing systems, and to assess whether significant repairs or maintenance were likely needed based on our visual, non-invasive inspection.
Forensic Water Intrusion Investigation Methodology
GCI approached the investigation with a structured, multi-phase methodology:
1. Project Document Review
To build a complete understanding of the building’s history and performance, GCI conducted a thorough review of key project documents. This included construction plans, shop drawings, as-built drawings, manufacturer specifications, test reports, maintenance records, and prior engineering evaluations. Our review provided critical insight into the original design intent, any modifications made over time, and patterns of recurring issues or repairs. Key documents — such as roof schematics, architectural elevations, exterior wall and window details, and wall sections — helped us pinpoint potential vulnerabilities in the building envelope system.
2. Site Inspection
GCI conducted a comprehensive, non-invasive visual inspection of the building’s exterior walls, roofing, and glazing systems. Observations were made from accessible exterior and interior areas, without the need for destructive testing or water infiltration testing. To support our findings, we captured high-resolution photographs and developed annotated diagrams, clearly documenting observed deficiencies such as failed sealant joints, physical damage to EIFS panels, and other critical vulnerabilities in the building envelope.
3. Investigative Report with Recommendations
Upon completion of the document review and site inspection, GCI prepared a detailed investigation report. The report documented:
- Findings from the document review and service history.
- Existing visible conditions and identified deficiencies.
- General opinions regarding the current condition of the exterior walls and glazing systems.
- Schematic recommendations for repairs or recommendations for further investigation or testing, where applicable.
The Results
GCI’s forensic water intrusion investigation revealed that water infiltration on the upper floors was primarily due to failure of the TPO roofing membrane and a lack of adequate drainage in the EIFS-clad parapet walls. In summary, these conditions allowed moisture to migrate into the building envelope, directly impacting the performance of the exterior walls and glazing systems.
Roof and Parapet Issues
The roof membrane exhibited punctures and seam failures, enabling water to penetrate the system. Water then traveled along the metal stud-framed parapet walls clad in face-sealed EIFS — an assembly that lacks a secondary drainage plane. Ultimately, this design flaw created a pathway for water to travel from the roof edge down into the window heads below, leading to localized interior damage and operational disruptions.
EIFS and Wall System Deficiencies

Single-ply roof in poor condition.
A visual inspection revealed multiple vulnerabilities across the exterior wall system, including:
- Failed and deteriorated sealant joints
- Physical damage to EIFS panels
- Unsealed penetrations
- Moisture behind EIFS, particularly above upper-floor windows
Consequently, the absence of a drainage mechanism within the EIFS system intensified the risk of moisture entrapment, leading to potential deterioration of interior finishes, sheathing, and wall framing. GCI recommended targeted destructive testing — especially at parapet walls — to assess concealed structural damage.
Glazing System Concerns
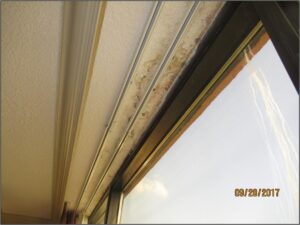
Water damage at head of window inside guest room.
Prior sealant repairs had unintentionally altered the original drainable ribbon window system into a barrier system, heightening reliance on perimeter sealants. Observed deficiencies included:
- Degraded metal-to-metal, metal-to-glass, and metal-to-EIFS sealants
- Water infiltration within insulating glass units
- Suspect organic growth on interior surfaces
Specifically, GCI recommended comprehensive sealant replacement using high-performance silicone sealants and advised consideration of full glazing system replacement with impact-rated assemblies to meet current code requirements and enhance long-term durability.
Recommendations for Remediation and Maintenance
To restore performance and minimize long-term risk, GCI recommended:
-
Staining observed under windows.
Immediate replacement of the compromised TPO roof with a high-reflectance, Energy Star-rated membrane
- Destructive testing and repair of EIFS-clad parapet walls to assess and restore structural integrity
- Replacement of all failed sealant joints throughout the envelope
- Application of a breathable, waterproof coating over EIFS surfaces
- Implementation of a phased, budget-conscious repair and maintenance plan
- Regular envelope inspections to preserve system performance
Additional Considerations
In conclusion, GCI recommended upgrading the existing glazing systems to help improve long-term building performance. Modern, impact-resistant assemblies offered enhanced resilience against windborne debris, improved energy efficiency, and could provide insurance and operational cost benefits. Additionally, we strongly recommended a proactive maintenance program be implemented to help extend the building’s service life, reduce lifecycle costs, and protect overall asset value.
Also for areas exhibiting signs of organic growth, GCI advised retaining a qualified third-party indoor air quality (IAQ) consultant. They would perform air and surface sampling, oversee remediation efforts, and provide post-remediation verification to ensure occupant health and safety.
Overall, our proposed repair strategy emphasizes building envelope durability, material efficiency, and long-term maintenance planning. While sustainability was not the primary focus, our recommended improvements — such as selecting long-lasting, efficient materials, improving air and moisture control, and considering recycled content where appropriate — supported broader sustainability goals.
For additional guidance on sustainable building envelope strategies, the WBDG guide on “Sustainability and the Building Envelope” offers a valuable overview of best practices. It covers key principles such as site optimization, indoor environmental quality, and preventative maintenance—many of which align with the recommendations presented in this case study.